Pharmaceutical and biotech production—such as reactor temperature control, vaccine storage, fermentation, and cleanroom monitoring—requires strict, traceable control of temperature, humidity, and other critical parameters to comply with GMP, FDA, and other regulatory standards. Equipment must operate reliably over extended periods and support multi-point data logging, alarm notifications, and system integration. Our high-precision controllers, paperless recorders, and communication modules help build compliant, secure, and fully monitored pharmaceutical environments.
Raw Material Dissolution
Raw material dissolution is a critical step in pharmaceutical manufacturing, used to homogenously dissolve and prepare APIs and excipients prior to formulation. It ensures dosage accuracy, content uniformity, and bioavailability. The process must adhere to strict controls on temperature, agitation, and hygiene, and comply with GMP standards.
The system can incorporate high-precision PID controllers to precisely regulate heating temperature and agitation speed. It supports CIP/SIP (Clean/Steam-in-Place) modules to prevent cross-contamination and ensure sanitary processing. Equipped with temperature, level, pressure, and flow sensors, and integrated with 21 CFR Part 11–compliant paperless recorders, the system logs all process data and alarms, enabling full batch traceability, production reporting, and quality audits.
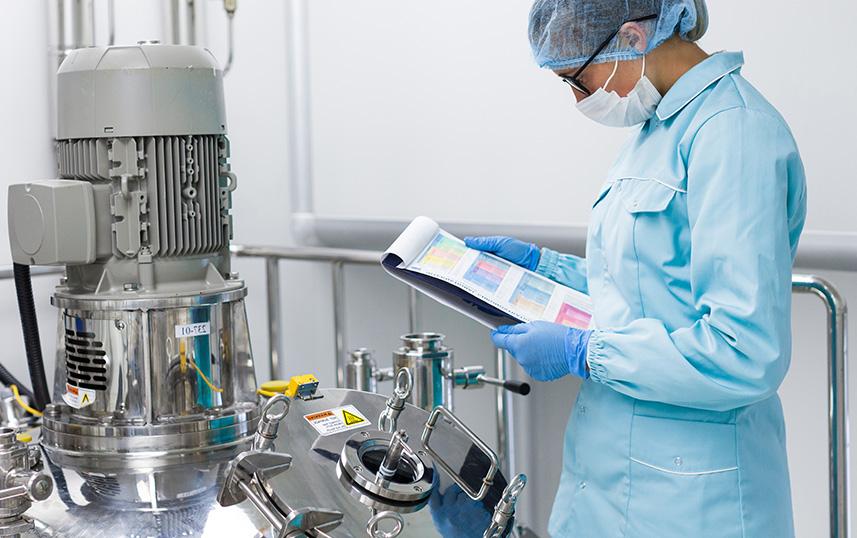
Dry Heat Sterilizer
A dry heat sterilizer uses high-temperature dry air circulation to sterilize instruments, glassware, metal tools, and items that cannot withstand moist heat sterilization. By maintaining a consistent temperature and duration, it denatures microbial proteins and cellular structures to achieve sterilization.
The system typically integrates a PID controller to precisely regulate heating elements and fan speeds, ensuring uniform and stable internal temperature. Equipped with temperature sensors and over-temperature protection, it prevents overheating and ensures safe operation. Coupled with a paperless recorder, detailed sterilization temperature profiles and times are logged for process traceability and quality control, complying with GMP requirements.
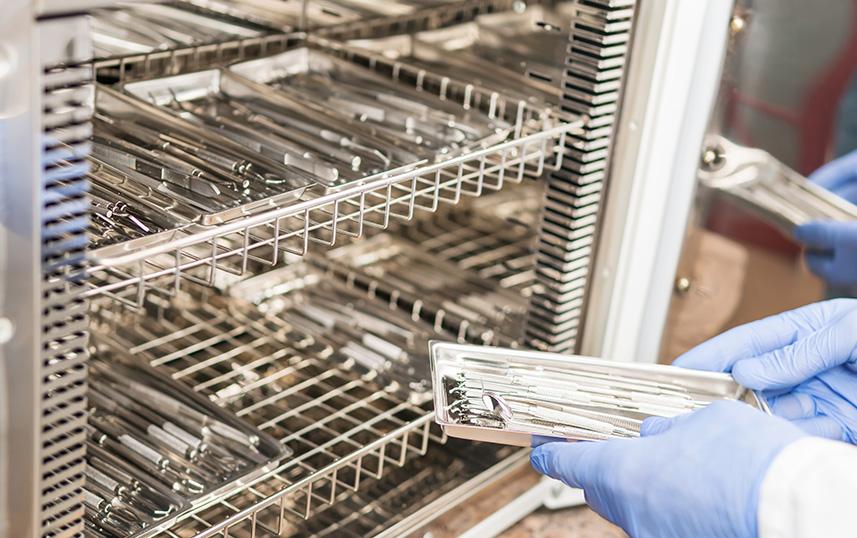
HTST
HTST sterilization is widely used in the pharmaceutical industry for aseptic processing of liquid drugs, sterile water for injection, and other heat-sensitive formulations. This method achieves effective sterilization in a short time, minimizing thermal degradation of active pharmaceutical ingredients, ensuring product safety and efficacy.
The system integrates high-precision PID controllers to precisely regulate temperature and flow in heating and cooling sections, maintaining compliance with stringent sterilization standards. Equipped with temperature, pressure, and flow sensors, it enables fully automated monitoring and fault protection to ensure process stability and reliability. A GMP and 21 CFR Part 11-compliant paperless recording system documents all process parameters and batch data for traceability and quality audits.
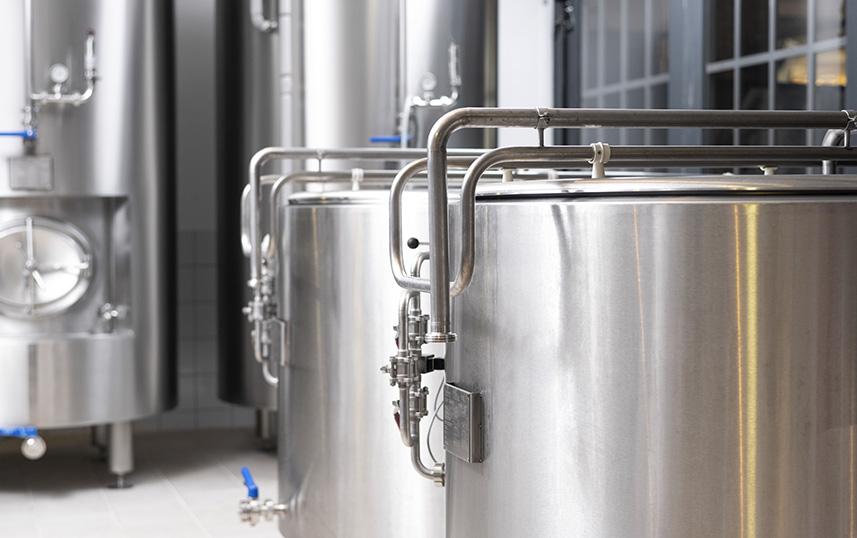
Bioreactor
A bioreactor is a closed system designed to provide a controlled environment for the cultivation and bioreaction of microorganisms, animal or plant cells, or enzymes. By precisely regulating temperature, pH, dissolved oxygen, agitation speed, and nutrient supply, it facilitates the efficient production of target products such as vaccines, antibodies, enzymes, or biopharmaceuticals.
The system typically includes PID controllers to accurately manage heating/cooling, gas flow control (oxygen, carbon dioxide, etc.), agitator motor speeds, and pH adjustment. Combined with various sensors (temperature, pH, dissolved oxygen, agitation speed) and automated monitoring, it ensures stable reaction conditions and real-time adjustments, enhancing bioreaction efficiency and yield. A paperless recorder provides comprehensive process parameter logging for process optimization, quality control, and regulatory compliance.
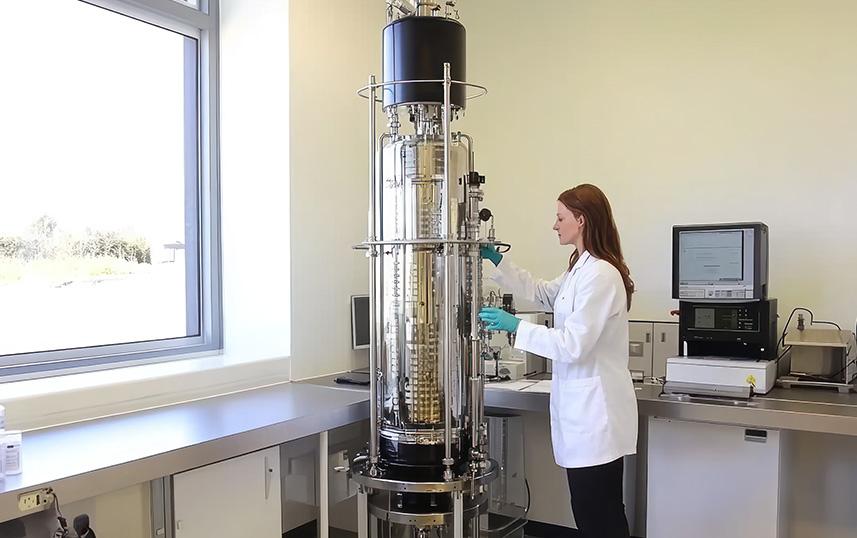