Plastic and rubber manufacturing processes—including injection molding, extrusion, and vulcanization—require strict temperature and pressure control to ensure dimensional stability and consistent material properties. Precise multi-stage temperature control and continuous data logging help prevent overheating, scorching, and material waste while improving product quality and production efficiency. Systems must support long-term operation and anomaly alarms to avoid costly process disruptions. Our high-performance temperature controllers and paperless recorders assist the plastics and rubber industries in optimizing processes and ensuring quality.
Plastic Injection Molding Machine
Plastic injection molding machines are essential for mass-producing plastic products such as housings, connectors, and containers. By melting plastic and injecting it into molds for cooling and shaping, they enable high-precision and high-efficiency manufacturing.
The system can be equipped with a PID controller to precisely regulate barrel zone heating and holding pressure, ensuring stable melt flow and plasticizing quality. It also allows synchronized control of injection speed, holding time, cooling duration, and mold open/close actions, enhancing product consistency and cycle efficiency. With integrated pressure, temperature, and position sensors, closed-loop control can be achieved. A paperless recorder can be used to log molding parameters and production trends for process traceability, fault diagnostics, and quality assurance.
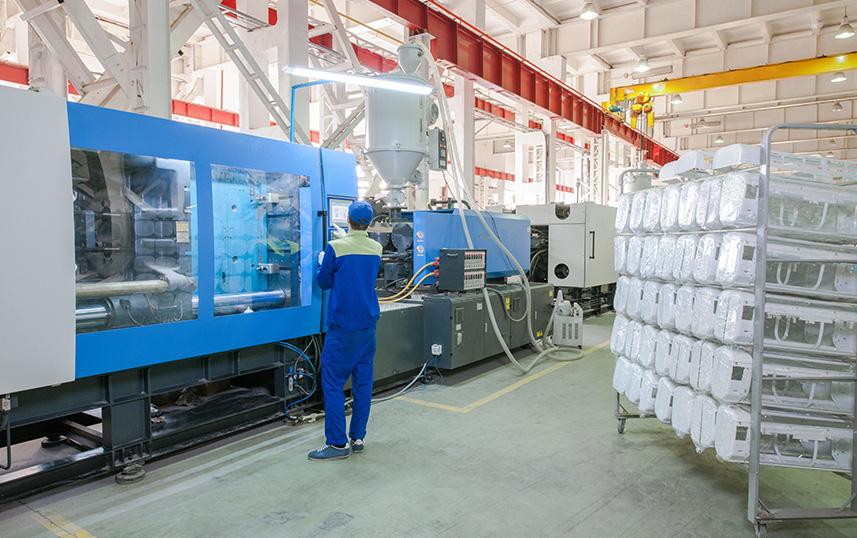