Water and wastewater treatment systems span multiple stages—from influent pre-treatment and biological reactions to disinfection, sludge drying, and final discharge. Each stage demands stable control of temperature and environmental conditions to ensure process efficiency, operational safety, and regulatory compliance. We offer a complete range of solutions, including high-precision PID controllers, multi-loop temperature systems, paperless recorders, and environmental data loggers, helping clients build robust, digital-ready treatment operations.
Bar Screen & Grit Chamber
(Pre-treatment System)
In water treatment processes, the pre-treatment stage serves to remove large solids and grit, protecting key downstream equipment and ensuring stable system performance.
A PID controller enables precise regulation of the discharge flow rate or pressure of lift pumps, helping to balance the influent load to subsequent units. When integrated with a PLC, the system can also automatically control the bar screen’s cleaning intervals and motor speed.
The system supports integration with flow meters, pressure sensors, and level sensors, and can be paired with a paperless recorder to log daily influent volume and equipment operation status. With trend charts and alarm history, the system helps optimize maintenance schedules and track anomalies effectively.
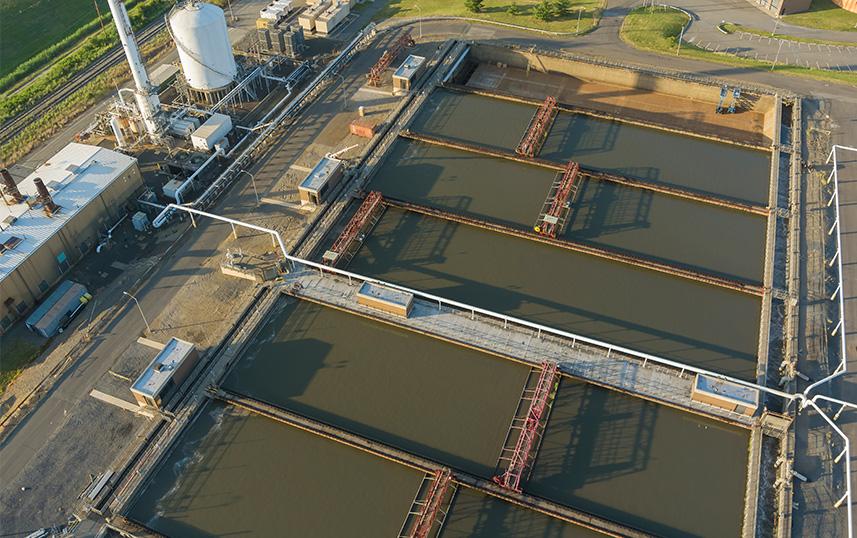
Primary Sedimentation Tank
In the primary treatment stage, the main objective is to remove settleable solids and a portion of organic matter, reducing the load on downstream treatment units and enhancing overall system efficiency.
Using a PID controller, the system can precisely adjust the scraper motor’s speed and operation cycle to prevent excessive sludge accumulation. Inlet and outlet valve flow control helps to avoid hydraulic overload and short-circuiting.
A paperless recorder can be integrated to continuously log key parameters such as suspended solids (SS), flow rates, tank level fluctuations, and operating time. These records support sedimentation efficiency analysis, trend tracking, and report generation, ensuring optimized operation and traceability.
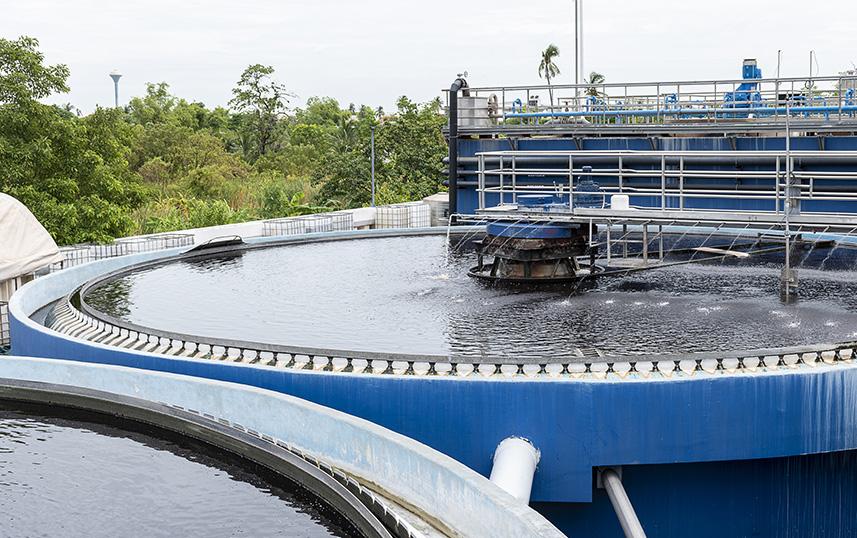
Aeration Tank
The aeration tank introduces continuous oxygen supply to promote microbial degradation of organic pollutants, playing a vital role in the biological treatment process.
A PID controller can be used to regulate blower air flow and maintain dissolved oxygen (DO) levels, ensuring optimal aerobic microbial activity. It also allows for precise control of return sludge pump flow to stabilize biomass concentration. For nutrient balance, chemical dosing pumps can be used to adjust the C:N:P ratio, enhancing microbial efficiency and treatment stability.
A paperless recorder can be integrated to monitor and log critical operational parameters such as DO, pH, MLSS (Mixed Liquor Suspended Solids), temperature, and flow rate. Historical trend analysis and alarm logs provide valuable insight for process optimization and fault diagnostics, and can also serve as traceable documentation for regulatory audits or internal management reviews.
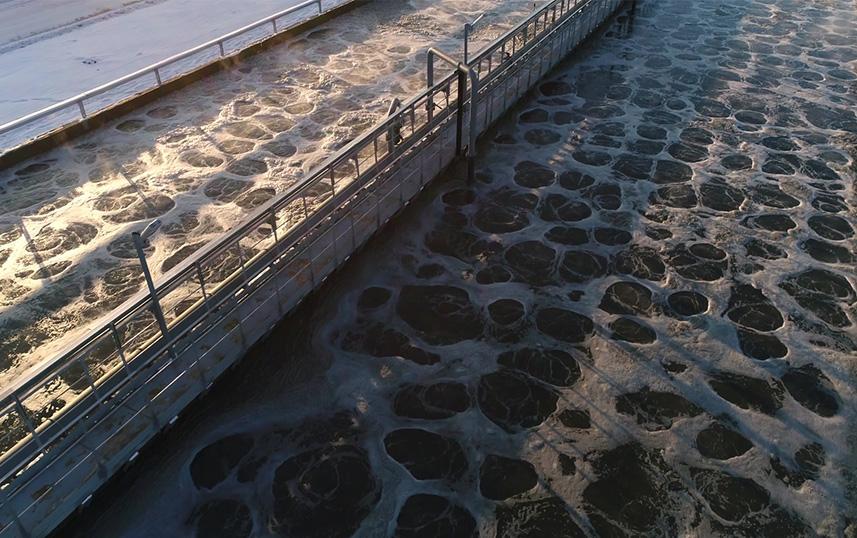
Chlorine Contact Tank
The chlorine contact tank ensures that residual chlorine has sufficient contact time with the water to complete the disinfection reaction, ensuring that the treated water complies with drinking water or discharge standards.
A PID controller can be used to precisely regulate the chlorine dosing rate, while feedback from a residual chlorine sensor allows for automatic adjustment of the chemical dosing pump frequency, maintaining stable residual chlorine levels and consistent disinfection performance.
A paperless recorder can be integrated to continuously log key data such as chemical dosing volume, residual chlorine concentration, and effluent flow rate, providing reliable records for disinfection validation, regulatory audits, and quality assurance tracking.
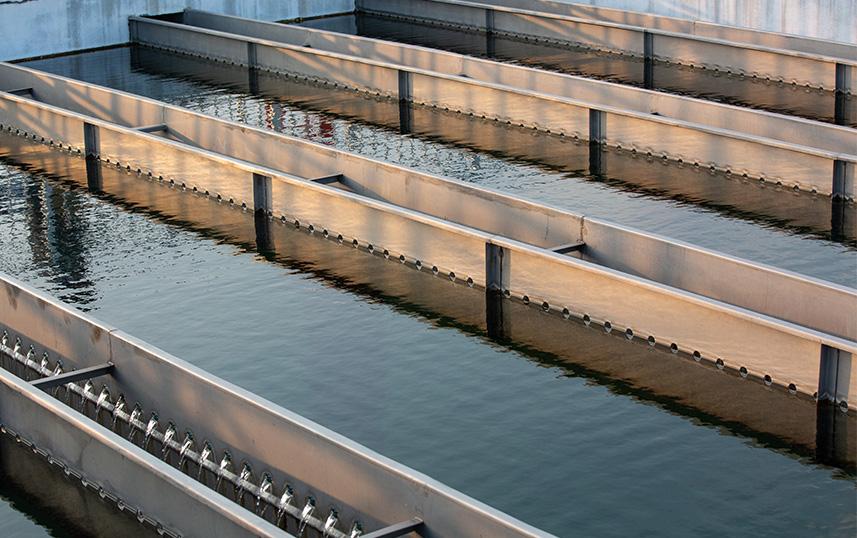
Heated Sludge Digester
(Aerobic or Anaerobic)
A heated sludge digester enhances microbial breakdown of organic matter by maintaining optimal temperature and mixing conditions, helping to reduce sludge volume and improve final disposal efficiency.
A PID controller can be employed to precisely regulate the digester temperature and mixing motor speed, whether in aerobic or anaerobic digestion systems. Stable temperature control improves microbial activity and digestion performance, ensuring a more efficient and consistent sludge treatment process.
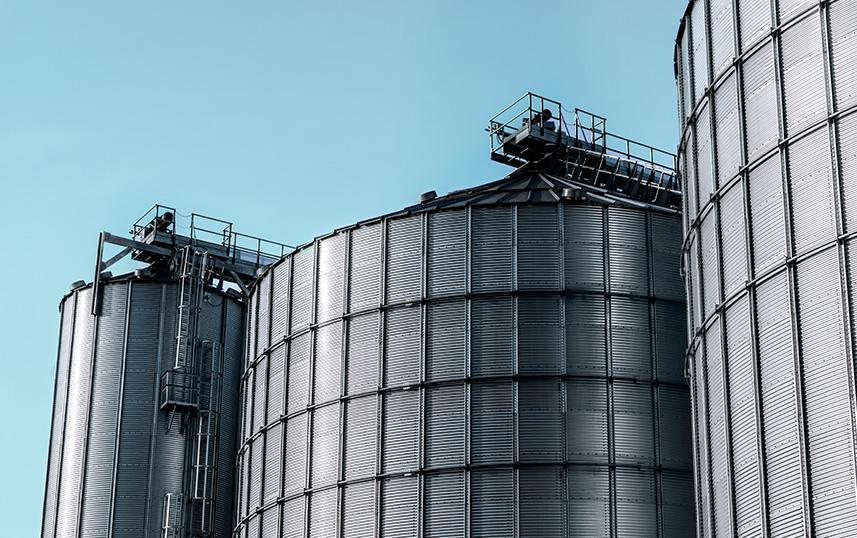