Features
- 96×96mm panel mount (1/4 DIN)
- Universal input: TC, RTD, mV, mA, voltage
- Dual 4-digit LED display for PV and SV
- 18-bit A/D converter for high resolution input
- Fast 5 samples/sec input sampling rate
- Auto/manual mode with bumpless transition
- Ramping function with adjustable slope rate
- Auto-tuning with fuzzy logic PID adjustment
- Digital filter to stabilize fluctuating signals
- Cold and warm start auto-tune supported
- Sensor break detection for process safety
- Lockout levels for parameter protection
- Configurable alarm: high, low, band, dwell
- Output 2 can be set as dwell timer function
- Relay, SSR, or analog output options
- Built-in Modbus RTU via RS-232 or RS-485
- USB programming port for PC-based setup
Modular PID Controller for Process Automation
Fuzzy PID, multi-output, RS-485, ramp/soak profile
This compact PID controller is designed to deliver reliable and intelligent temperature or process control for a wide range of industrial applications. Featuring universal input compatibility, a high-resolution 18-bit A/D converter, and multiple output options such as relay, SSR voltage drive, or analog signal, it offers flexibility for both basic and advanced control environments.
The controller integrates fuzzy logic auto-tuning, supports RS-232 and RS-485 Modbus RTU communication, and includes a ramp/soak program with dwell timer, making it ideal for precise, automated control in OEM equipment, production lines, and control panels.

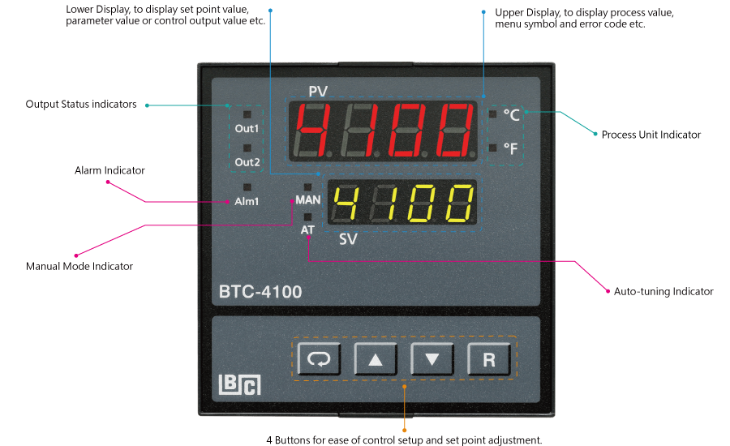
LED Display Panel with Simple Key Control
Clear indicators and tactile keypad ensure easy operation
The front panel interface features a bright dual 4-digit LED display, providing real-time feedback of process value (PV) and set value (SV) simultaneously. This high-contrast display ensures clear visibility even in low-light industrial environments.
Multiple status indicators are clearly arranged to present operating conditions at a glance, including:
-
Output activity
-
Alarm state
-
Auto-tuning (AT) status
-
Manual mode (MAN)
-
Engineering unit display (UNIT)
These indicators help users monitor the control state with minimal effort, enhancing situational awareness and reducing errors during setup or adjustments.
The controller includes a tactile keypad with four intuitive buttons: Scroll, Up, Down, and Enter. The keys provide positive feedback for each press and support smooth navigation across parameter settings. This layout makes the controller easy to operate even in space-constrained panels or time-critical applications, improving work efficiency on the shop floor.
Universal Input Support with High Accuracy
Accepts TC, RTD, mV, mA and voltage signals
The controller supports universal input signals, including:
-
Thermocouple: J, K, T, E, N, R, S
-
RTD: Pt100 DIN / JIS
-
Analog: 0–50 mV, 0–20 mA, 4–20 mA, 0–5V, 1–5V
Equipped with an 18-bit A/D converter, the input circuitry offers high accuracy, fast 5Hz sampling rate, and cold junction compensation for thermocouples. Signal stability is further enhanced by digital filtering and sensor break detection, ensuring safe, reliable operation in demanding process environments.
Flexible Output Choices for Any Control Need
Relay, SSR, and analog output types are selectable
The controller offers multiple output options for control and alarm use:
-
Relay contact: 250 VAC / 2A
-
SSR voltage drive: 12 VDC ±15%, 30 mA max
-
Analog output: 0–20 mA, 4–20 mA, 0–10 V, 1–5 V
Analog outputs are generated via a 15-bit D/A converter, ensuring high-resolution retransmission and smooth signal control. Each output channel can be independently configured for PID control, alarm logic, or dwell timer functions, providing great flexibility in system integration.
Fuzzy PID Technology
Smarter Control with Less Overshoot and Faster Response
Fuzzy logic is combined with traditional PID control to deliver smarter and more adaptive temperature regulation. Unlike standard PID controllers that require manual fine-tuning for each application, fuzzy PID dynamically adjusts control responses based on real-time process behavior. The result is faster stabilization, reduced overshoot, and improved resilience to disturbances—ideal for processes where precision and speed are critical.
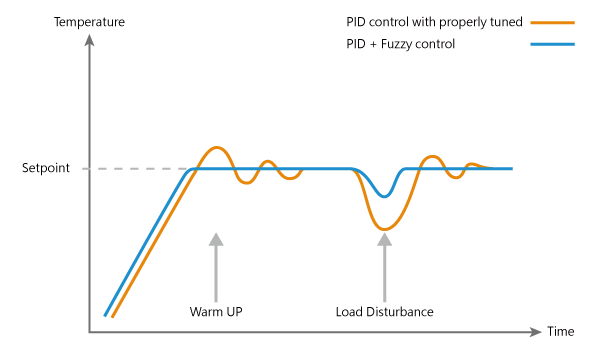
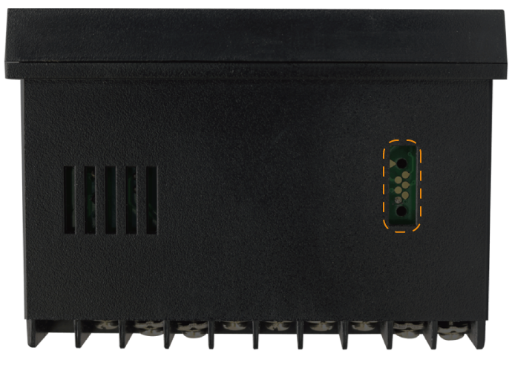
Dedicated Programming Port for Easy Setup
Touch-port with special cable for offline configuration
The controller features a dedicated touch-type programming port, designed for use with the CC91-1 programming cable. This port allows fast and reliable offline parameter setup, calibration, and ATE-based testing, connecting to a PC or automated test equipment without accessing the main terminals.
To ensure system integrity, this port is intended for setup and testing only. It should be disconnected during normal operation. Optional adapters such as the SNA12A can convert this port for RS-232 communications if required.
BC-SET Pro Configuration Software
Easy parameter setup, backup and firmware upgrade
BC-SET Pro is the official configuration software developed by BrainChild for its over-temperature protection controllers. With a streamlined and intuitive interface, the software allows users to connect via USB programming cable and quickly configure control parameters. It supports efficient parameter editing, setting duplication between devices, and firmware upgrades to maintain device performance and stability. BC-SET Pro also enables offline configuration with the ability to save and manage multiple profiles, making it ideal for production environments, system deployment, and ongoing maintenance. Whether for new setup or existing system adjustment, this tool helps engineers and technicians simplify workflow, reduce setup time, and ensure consistent configuration across all devices.
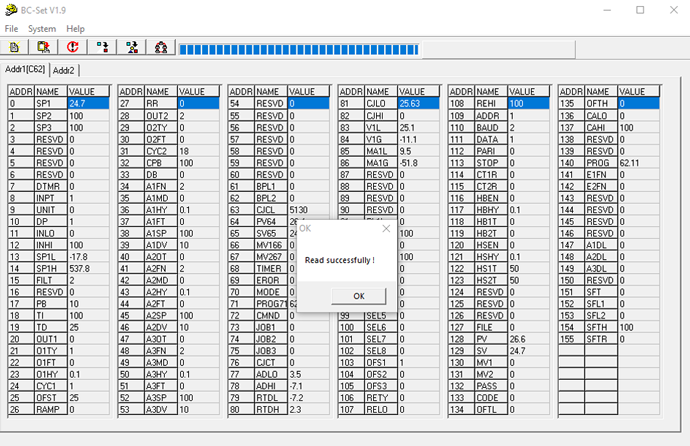
Batch Read/Write for Multiple Controllers
BC-SET allows users to connect multiple controllers of the same model and perform batch parameter read/write by defining a node address range. This feature significantly streamlines configuration in OEM or multi-device environments.
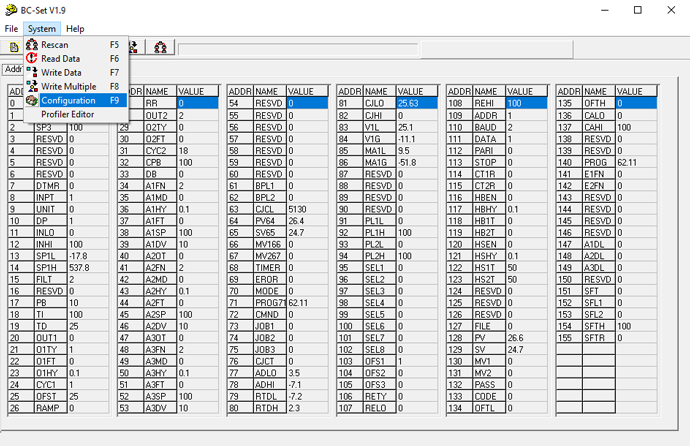
Clear and Accessible System Menu
The system menu offers quick access to key operations like Rescan (F5), Read Data (F6), Write Data (F7), Write Multiple (F8), and Communication Settings (F9). Built-in hotkeys support fast, efficient navigation.
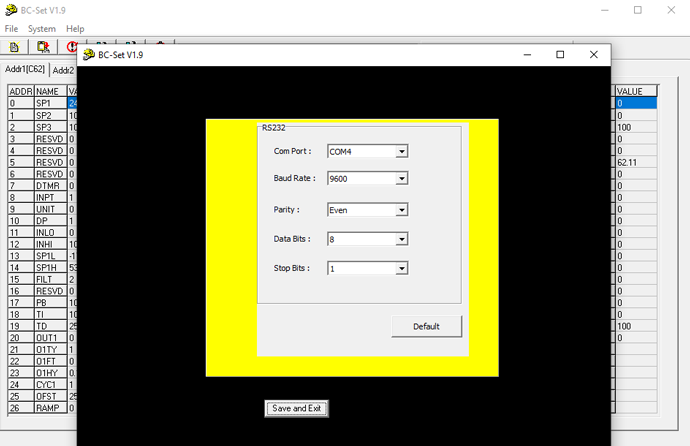
Intuitive Communication Setup Interface
The communication settings window lets users define COM port, baud rate, parity, data bits, and stop bits — with a “Default” button for quick reset and “Save and Exit” to finalize setup. Designed to reduce setup errors.
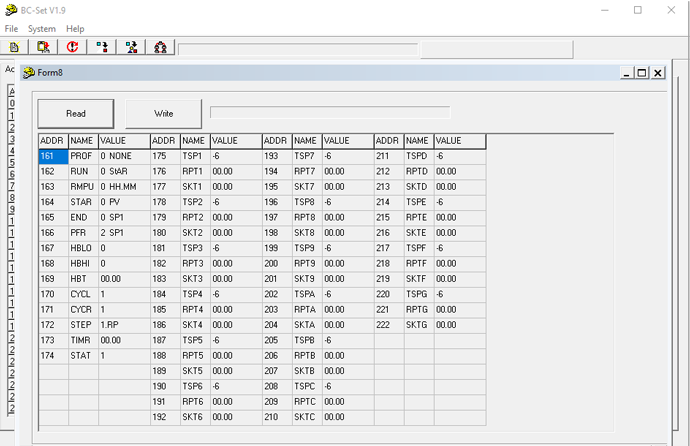
Visual Profile Editor for Programmable Controllers
For controllers with profile functionality, BC-SET provides a graphical editor to configure temperature ramp/soak segments. Users can easily read, modify, and write profile parameters for precise thermal process control.
Standard IP50 Panel, Optional IP65 Upgrade
Terminals IP20; suitable for indoor applications only
The controller's standard front panel protection is IP50, offering basic shielding against solid particles. For higher protection, an optional water-resistant rubber seal can be installed, upgrading the panel rating to IP65, ideal for use in environments with dust or water spray.
The housing and terminal block are rated IP20, providing minimal ingress protection. The unit is designed for indoor use only, and should be installed inside a protective enclosure for long-term reliability and safety in industrial control systems.
Applications
Specification
Power
Signal Input
Output 1 / Output 2
Linear Output
Triac ( SSR ) Output
Alarm
Data Communication
Analog Retransmission
User Interface
Control Mode
Digital Filter
Environmental and Physical Specifications
Approval Standards
Download
Visit Download Center to See More Documents & Tools of This Product. Visit
FAQ
The controller supports thermocouple (J, K, T, E, N, R, S), RTD (Pt100 DIN/JIS), and analog signals such as mV, mA, and voltage (0–5V, 1–5V).
The standard panel is IP50. IP65 protection is available as an optional accessory by installing a water-resistant rubber gasket.
No. The programming port is for offline setup and testing only. It must be disconnected during normal operation.
The controller supports RS-232 or RS-485 Modbus RTU communication as optional configurations.
Yes. It supports multi-segment ramp/soak profile programming with dwell timer for precision process control.