Features
- Compact 48x48mm DIN panel mount design
- High-accuracy universal input for T/C, RTD, mV
- Supports 18-bit resolution and 3Hz sampling rate
- Auto-tuning and manual PID adjustment supported
- Single-stage ramp and dwell timer function
- Configurable control output: Relay, SSR, Analog
- Selectable linear current or voltage output
- Alarm output with flexible logic options
- Sensor break detection and safety protection
- Intuitive 4-key interface for easy setup
- Dual LED display for PV and SV monitoring
- Supports heating/cooling or ON-OFF control
- Optional RS-485/RS-232 for communication
- User-configurable parameters and hysteresis
- Wide power range: 90–264VAC or 20–32VDC
BTC-9090 Fuzzy PID Controller for Compact Installations
The BTC-9090 is a microprocessor-based temperature controller designed for compact panel applications. Featuring fuzzy logic-enhanced PID control, the BTC-9090 ensures rapid set point attainment with minimal overshoot. It supports a wide range of thermocouples, RTDs, and linear signals, and offers both automatic and manual tuning modes for optimal flexibility. Ideal for applications requiring ramp/soak cycles, soft-start control, and precise process stabilization.
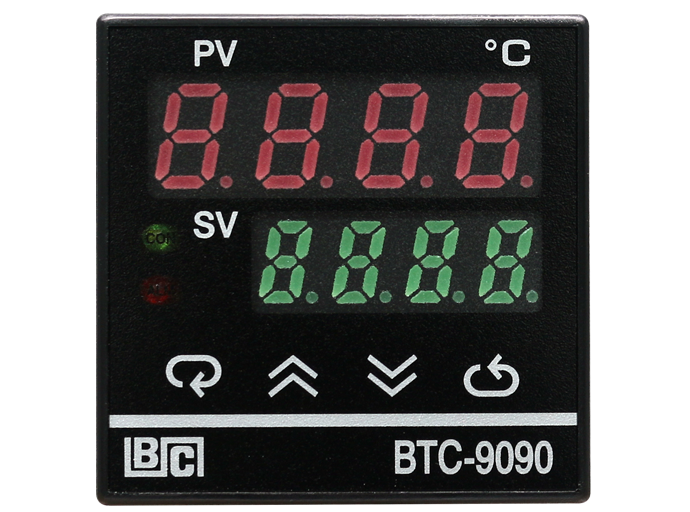
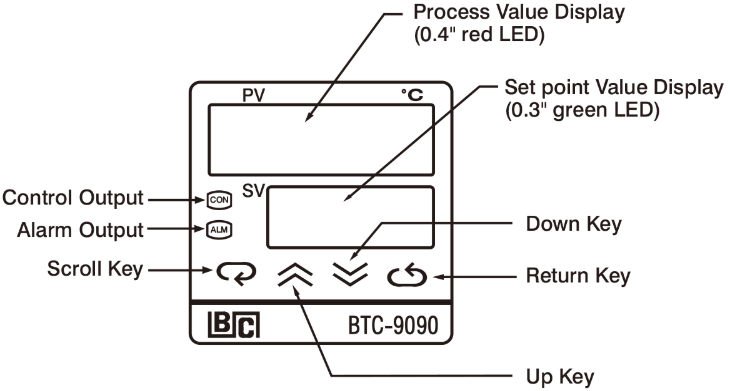
LED Display & 4-Key Compact Panel Control
Easy navigation with dual-display and intuitive keypad
The BTC-9090 features a compact 48×48mm front panel with a clear dual 4-digit LED display. The top line shows the process value (PV) and the bottom line shows the setpoint value (SV), allowing for quick reference during operation.
The front panel is equipped with four tactile keys:
-
UP / DOWN for value adjustment
-
SCROLL for parameter navigation
-
RETURN / ENTER to confirm or cancel entries
This layout enables easy setup and quick parameter access, even in tight installation spaces. The bright display ensures visibility under various lighting conditions.
Universal Input for T/C, RTD, mV & Voltage
High-accuracy A/D with wide signal compatibility
BTC-9090 accepts a broad range of universal input types, including:
-
Thermocouple: J, K, T, E, N, R, S
-
RTD: Pt100 DIN / JIS
-
Linear: 0–50 mV, 0–5 V, 1–5 V
The unit uses a high-resolution 18-bit A/D converter with a sampling rate of 3Hz, delivering stable readings and precise process control. Cold junction compensation and digital filtering ensure input signal integrity even under industrial conditions.
Flexible Output Choices for Any Control Need
Relay, SSR, and analog output types are selectable
The controller offers multiple output options for control and alarm use:
-
Relay contact: 250 VAC / 2A
-
SSR voltage drive: 12 VDC ±15%, 30 mA max
-
Analog output: 0–20 mA, 4–20 mA, 0–10 V, 1–5 V
Analog outputs are generated via a 15-bit D/A converter, ensuring high-resolution retransmission and smooth signal control. Each output channel can be independently configured for PID control, alarm logic, or dwell timer functions, providing great flexibility in system integration.
Fuzzy PID Technology
Smarter Control with Less Overshoot and Faster Response
Fuzzy logic is combined with traditional PID control to deliver smarter and more adaptive temperature regulation. Unlike standard PID controllers that require manual fine-tuning for each application, fuzzy PID dynamically adjusts control responses based on real-time process behavior. The result is faster stabilization, reduced overshoot, and improved resilience to disturbances—ideal for processes where precision and speed are critical.
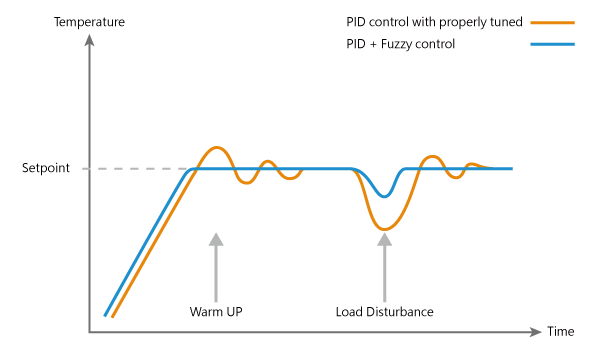
Applications
Specification
Power
Signal Input
Output 1 / Output 2
Linear Output
Triac ( SSR ) Output
Alarm
Data Communication
Analog Retransmission
User Interface
Control Mode
Digital Filter
Environmental and Physical Specifications
Approval Standards
Download
Visit Download Center to See More Documents & Tools of This Product. Visit
FAQ
The controller supports thermocouple (J, K, T, E, N, R, S), RTD (Pt100 DIN/JIS), and analog signals such as mV, mA, and voltage (0–5V, 1–5V).
The standard panel is IP50. IP65 protection is available as an optional accessory by installing a water-resistant rubber gasket.
No. The programming port is for offline setup and testing only. It must be disconnected during normal operation.
The controller supports RS-232 or RS-485 Modbus RTU communication as optional configurations.
Yes. It supports multi-segment ramp/soak profile programming with dwell timer for precision process control.